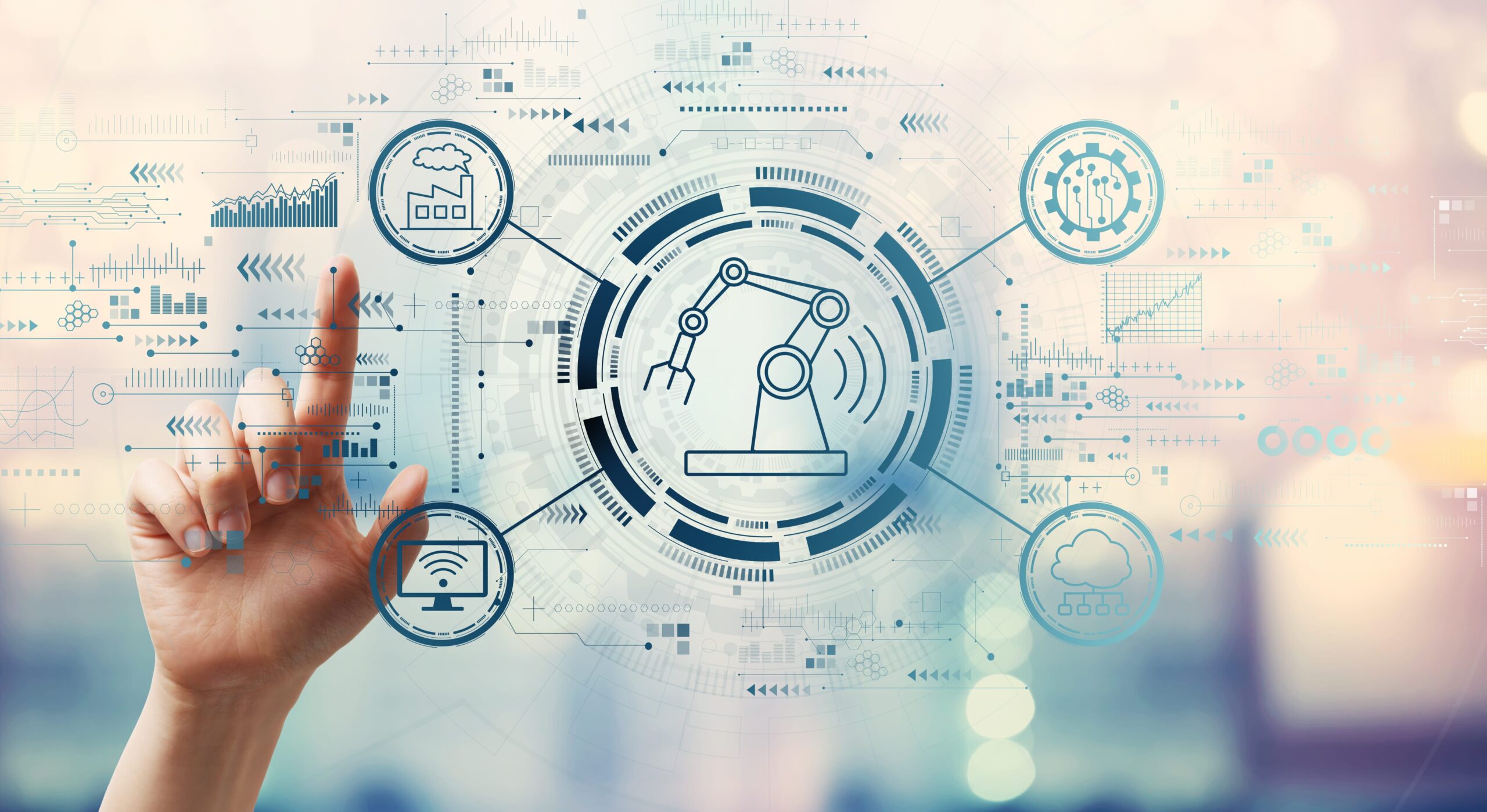
The manufacturing sector is undergoing a green revolution, driven by significant strides in eco-friendly materials and energy-efficient processes. However, this transformation extends far beyond the materials and means of production to reach the very technologies that drive manufacturing innovation.
From smart factories utilizing IoT for optimized resource management to AI-driven predictive maintenance systems, these innovations are reshaping the landscape. Embracing these trends will not only enhance sustainability; it will also boost efficiency and productivity, highlighting the pivotal role of innovation in manufacturing for a more sustainable future.
Understanding the Need for Sustainable Manufacturing
Manufacturing processes have historically been significant contributors to environmental degradation, producing large quantities of greenhouse gasses, waste, and pollution. Sustainable manufacturing aims to reduce these negative impacts by adopting practices that conserve resources and minimize environmental footprints. Implementing sustainable manufacturing processes can significantly cut down on carbon emissions and waste, promoting a healthier planet.
Sustainability in manufacturing is not only beneficial for the environment but also offers substantial economic advantages. Companies that adopt sustainable practices often experience reduced operating costs due to increased efficiency and lower waste production. Furthermore, sustainable products meet the growing consumer demand for environmentally friendly options, potentially leading to higher sales and improved brand loyalty.
Barriers to Innovation in Green Manufacturing
Despite the clear benefits, several barriers hinder the widespread adoption of sustainable manufacturing practices. Understanding these obstacles is crucial for developing strategies to overcome them and foster a more sustainable industrial landscape.
Skilled Labor Shortage
One of the primary challenges in implementing sustainable manufacturing practices is the lack of skilled labor. Finding qualified personnel with the expertise to develop, manage, and maintain these innovative systems can be difficult, thereby hindering the progress of green initiatives.
Supply Chain Complexity
Ensuring responsible sourcing of materials and minimizing waste throughout the supply chain adds another layer of complexity to sustainable manufacturing. Manufacturers must navigate intricate supply chains to source eco-friendly materials and implement practices that reduce waste, requiring significant coordination and transparency.
Rapidly Evolving Regulations
Environmental regulations are continually evolving, adding pressure on manufacturers to adapt quickly. Keeping pace with these changes requires flexibility and foresight, as non-compliance can result in penalties and damage to a company’s reputation.
5 Trends Driving Green Innovation in Manufacturing
The integration of advanced technologies and sustainable practices is reshaping the manufacturing industry, leading to more eco-friendly and efficient production processes. Here are five key trends driving this transformation.
1. Smart Factories: The Backbone of Eco-Friendly Manufacturing
Digital Twins and Simulation: Smart factories leverage digital twins – virtual replicas of physical assets – to simulate and optimize production processes. These digital counterparts enable manufacturers to predict equipment failures and schedule maintenance proactively, significantly reducing energy consumption and waste. By optimizing operational efficiency, digital twins play a crucial role in enhancing sustainability and driving manufacturing innovation. [Deloitte] [Future of Commerce]
Advanced Robotics and Automation: Another pillar of smart factories is advanced robotics and automation. Collaborative robots, or cobots, work alongside human operators to enhance precision and efficiency. These technologies streamline processes and minimize human error, leading to significant reductions in energy usage. Automated systems ensure consistent production quality while optimizing resource utilization, contributing to more sustainable innovation in the manufacturing industry. [Genpact] [Future of Commerce]
2. Autonomous and Networked Supply Chains
Supply Chain Visibility: Autonomous supply chains, powered by artificial intelligence (AI) and the Internet of Things (IoT), provide real-time visibility into supply chain operations. This enhanced visibility enables manufacturers to respond swiftly to disruptions, optimize inventory levels, and reduce waste. Real-time data allows for better decision-making, ensuring a more resilient and sustainable supply chain—a hallmark of innovation in manufacturing.[Genpact] [Future of Commerce]
Circular Economy: Implementing circular economy principles in supply chain management ensures that products and materials are reused and recycled, minimizing waste and conserving resources. This approach aligns with global sustainability efforts, promoting the reuse of materials and reducing the environmental impact of production and consumption. [Future of Commerce] [Manufacturing Digital]
3. Artificial Intelligence: Optimizing Processes and Predicting Problems
Predictive Maintenance: AI algorithms analyze sensor data from machines to predict potential failures before they occur. This proactive approach to maintenance prevents costly downtime and reduces unnecessary energy consumption from running faulty equipment. Predictive maintenance ensures that machines operate at peak efficiency, contributing to overall energy savings. (參考 AI Applications in Manufacturing Industry)
Process Optimization: AI can scrutinize production line data to identify bottlenecks and inefficiencies to promote further innovation in manufacturing. By recommending adjustments to machine settings and production speeds, AI optimizes processes to reduce energy consumption and increase output. This level of optimization not only boosts productivity but also supports sustainable practices.
Yield Management: AI helps optimize material usage and minimize waste by analyzing historical data and production parameters. It predicts the optimal amount of raw materials needed for each product, reducing waste and the environmental impact of material acquisition. Yield management through AI ensures that resources are used efficiently and sustainably.
4. Industrial IoT: Gathering Real-Time Data for Informed Decisions
Energy Monitoring: The Industrial Internet of Things (IIoT) empowers manufacturers with real-time energy monitoring capabilities. IIoT sensors track energy consumption across various machines and processes, providing valuable insights into areas of high energy usage. This data enables manufacturers to prioritize efficiency improvements, leading to significant energy savings and a smaller environmental footprint.
Smart Grid Integration: Factories equipped with IIoT can integrate with smart grids, allowing for dynamic adjustments in energy consumption based on real-time grid conditions. By leveraging off-peak hours for energy-intensive processes, manufacturers can reduce reliance on peak grid usage, resulting in lower energy costs and a more balanced energy distribution.
Remote Monitoring and Control: IIoT facilitates remote monitoring and control of production lines, enabling manufacturers to swiftly identify and address potential issues such as equipment malfunctions or inefficiencies. This proactive approach prevents unnecessary energy waste and ensures smooth, continuous operations, contributing to overall sustainability.
5. Edge Computing: Processing Data Closer to the Source
Faster Decision-Making: Edge computing revolutionizes innovation in manufacturing by processing sensor data locally, close to the source. This real-time processing capability allows for quicker decision-making regarding energy use and process optimization. Manufacturers can react to changes instantaneously, minimizing energy waste and enhancing operational efficiency.
Reduced Network Bandwidth: By processing data at the edge, manufacturers reduce the need for extensive data transmission to the cloud. This not only improves efficiency but also minimizes the energy consumption associated with data transfer. Edge computing thus supports a more sustainable data management approach.
Improved Security: Processing sensitive data locally on edge devices enhances security by reducing dependence on cloud-based storage and transmission. This localized approach mitigates potential data breaches and ensures the integrity of critical manufacturing data, promoting a secure and sustainable production environment.
The Future of Sustainable Manufacturing
The future of sustainable manufacturing looks promising, driven by emerging technologies and increased collaboration within the industry.
Technologies such as quantum computing and blockchain are poised to revolutionize the sector by offering new methods to optimize processes, enhance transparency, and ensure eco-friendly practices. Quantum computing can solve complex problems faster, leading to more efficient resource usage and reduced waste. Meanwhile, blockchain can provide a secure and transparent way to track the sustainability of supply chains, ensuring that every step of the manufacturing process adheres to environmental standards.
Collaboration across the manufacturing industry will be crucial in this evolution. By sharing best practices and technological innovations, manufacturers can collectively work towards a more sustainable future. This cooperative approach will help the industry meet global sustainability goals and create a more resilient and environmentally responsible manufacturing landscape.
Platforms like entrapeer facilitate these collaborations by connecting enterprises with innovative startups and providing AI-powered insights that drive strategic decisions. [Deloitte] [Genpact]
Explore the Entrapeer Platform
The recent advancements in green manufacturing are paving the way for a more sustainable future. However, achieving these goals requires more than individual efforts; it necessitates a collaborative approach across the entire manufacturing industry. By working together and sharing knowledge, manufacturers can significantly enhance their sustainability practices and drive manufacturing innovation.
One effective way to foster such collaboration is through platforms like entrapeer. We encourage readers to sign up and explore the entrapeer platform to connect with like-minded professionals and discover new ways to drive sustainability.
Contact us today to learn more about how entrapeer can help you and your organization contribute to a greener, more sustainable future.
Ready to revolutionize your corporate innovation journey?
Create an account with entrapeer today to explore all the features of our enterprise innovation platform or contact us to learn more about how we can help you find the right startup partners and propel your innovation forward. Kick off your next POC in minutes and stay ahead of the curve in the fast-paced world of corporate innovation.
FAQs
Green innovation in manufacturing involves adopting new technologies and processes to make production more sustainable. This includes reducing waste, conserving energy, and using eco-friendly materials to minimize environmental impact.
Sustainable manufacturing is crucial for reducing the environmental impact of production processes, which includes cutting down on greenhouse gas emissions and waste. It also offers economic benefits, such as cost savings through increased efficiency and meeting consumer demand for environmentally friendly products.
Consumers influence sustainable manufacturing by demanding eco-friendly products and supporting brands that prioritize sustainability. Manufacturers respond to this demand by adopting greener practices to attract and retain environmentally conscious customers.
Examples include using renewable energy sources, implementing zero-waste policies, and employing biodegradable materials. Innovations like 3D printing with recycled materials and closed-loop systems also exemplify sustainable manufacturing practices.
Companies can measure success through key performance indicators (KPIs) such as energy consumption, waste reduction, and carbon footprint. Regular audits and sustainability reports can track progress and identify areas for improvement.